How to bleach palm oil is a critical process in the global palm oil industry. This comprehensive guide delves into the intricate steps, from the fundamental principles of bleaching to advanced optimization techniques. Understanding the process is vital for maximizing yield, ensuring product quality, and minimizing environmental impact.
The process involves a range of steps, from selecting appropriate bleaching agents to managing equipment effectively. We’ll examine the chemistry behind the process, the role of various equipment, and the crucial role of quality control. This guide also addresses the environmental considerations and safety precautions necessary for a responsible operation.
Introduction to Palm Oil Bleaching: How To Bleach Palm Oil
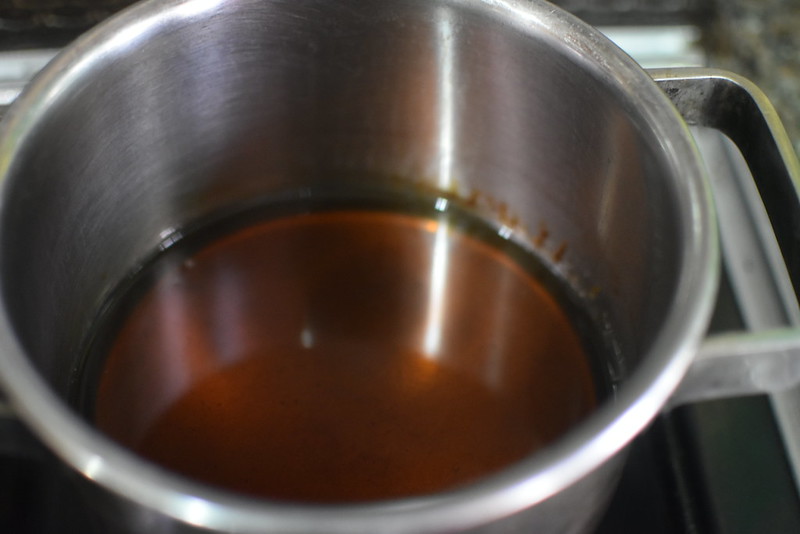
Palm oil, a ubiquitous ingredient in food and consumer products, requires processing to achieve desired qualities. Bleaching is a crucial step in this process, significantly impacting the final product’s color, appearance, and stability. This refining stage removes impurities and unwanted pigments, resulting in a more palatable and commercially viable product.
The bleaching process is vital for palm oil’s marketability. Unbleached palm oil often exhibits a darker color and a less desirable aesthetic, limiting its applications. Furthermore, bleaching enhances the oil’s stability by removing compounds that can lead to discoloration, rancidity, and off-flavors during storage and use.
Purpose of Bleaching Palm Oil
Bleaching is the removal of impurities, including pigments, color bodies, and other contaminants, from palm oil. This process is essential for achieving a consistent, light-colored product suitable for a wide range of applications. The light color is crucial for food and cosmetic products where visual appeal is paramount. Bleaching also improves the oil’s stability, preventing rancidity and extending its shelf life.
General Process of Bleaching
The bleaching process typically involves several stages. First, the palm oil is filtered to remove large impurities. Then, it’s treated with bleaching earth, a finely ground clay or other adsorbent material. The bleaching earth absorbs the impurities, effectively lightening the oil. Subsequent stages involve washing and filtration to remove the bleaching earth and ensure a pure product. The entire process is carefully monitored to maintain the desired quality and consistency.
Types of Bleaching Methods
Various bleaching methods are employed in the palm oil industry, each with its own advantages and disadvantages.
- Chemical Bleaching: This method uses chemical agents to remove impurities. While effective, chemical bleaching can sometimes introduce unwanted byproducts into the oil, potentially impacting its quality and safety. The choice of chemical agent is critical, as different agents have different effectiveness and safety profiles.
- Physical Bleaching: This approach employs physical methods like filtration and adsorption to remove impurities. It is generally considered a more environmentally friendly option, as it does not introduce chemicals into the product. The effectiveness of physical bleaching often depends on the specific filter and adsorption materials used.
- Combined Bleaching: This method combines chemical and physical bleaching techniques. This approach leverages the strengths of both methods, offering a balance between efficiency and environmental considerations. Combined bleaching often yields optimal results, but the specific combination of methods can vary depending on the desired outcome.
History of Bleaching Techniques in Palm Oil Production
The development of bleaching techniques in palm oil production has evolved significantly over time. Early methods relied on simple filtration techniques, which were not as effective in removing all impurities. The introduction of bleaching earth, a more sophisticated approach, significantly improved the quality and consistency of the final product. Modern bleaching processes often incorporate advanced filtration and purification technologies, ensuring optimal results while minimizing environmental impact. Technological advancements in refining processes continue to refine the quality of bleached palm oil.
Factors Affecting Bleaching Effectiveness
The efficiency of the bleaching process depends on several factors, including the type of bleaching earth used, the temperature and pressure conditions during treatment, and the quality of the palm oil itself. Variations in these factors can lead to differences in the final product’s color, clarity, and overall quality.
Equipment Used in Bleaching
Palm oil bleaching, a crucial step in refining, relies heavily on specialized equipment. The choice of equipment significantly impacts the efficiency, quality, and cost of the final product. Different stages of the process require tailored equipment, reflecting the diverse nature of the bleaching agents and the varying properties of palm oil.
The selection of bleaching equipment is a complex process. Factors such as the capacity of the facility, the desired level of purity, and the specific type of bleaching agents employed must be considered. Optimizing the equipment configuration ensures the most efficient removal of impurities, resulting in a higher-quality final product. Furthermore, minimizing downtime and maximizing throughput are key considerations in choosing the right bleaching equipment.
Types of Bleaching Equipment
Various types of equipment are employed in the palm oil bleaching process, each with its unique capabilities. These include filter presses, centrifuges, and various types of bleaching earth reactors. The choice depends on factors such as the desired throughput, the level of purity required, and the budget constraints.
- Filter Presses: These equipment types utilize filter cloths to separate the bleaching earth from the palm oil. They are effective in removing solid impurities and are often used in the initial stages of the bleaching process. Filter presses are typically preferred for their simplicity and reliability, especially for smaller-scale operations.
- Centrifuges: Centrifuges separate solid particles from the liquid palm oil based on density differences. They are frequently used in the later stages of the bleaching process, enhancing the efficiency of removing fine particles and suspended matter. Centrifuges offer a higher throughput compared to filter presses, especially for larger-scale operations.
- Bleaching Earth Reactors: These reactors are specifically designed to facilitate the interaction between palm oil and the bleaching earth. The reactors ensure proper mixing and provide the necessary contact time for optimal bleaching results. Different reactor designs, such as continuous or batch systems, offer varying levels of efficiency and control.
Stages of Bleaching Using Equipment
The bleaching process typically involves several distinct stages, each utilizing specific equipment. A well-designed process sequence maximizes the efficiency of removing impurities and produces a refined palm oil product.
- Pre-treatment: This stage involves the preparation of the palm oil for bleaching. This includes processes such as heating and degumming, often using specialized equipment like preheating coils and degumming units. The goal is to remove impurities like gums and other contaminants before the actual bleaching process begins. The quality of pre-treatment significantly affects the effectiveness of the subsequent stages.
- Bleaching: This is the core stage, where the palm oil is treated with bleaching earth in the bleaching earth reactors. The contact time and temperature are carefully controlled to ensure efficient removal of impurities. The choice of bleaching earth is crucial in this stage, influencing the final quality and purity of the palm oil.
- Washing/Filtration: After the bleaching process, the palm oil is washed to remove any residual bleaching earth. This is often done using filter presses or centrifuges to remove the bleaching earth from the oil. Proper washing ensures the final product is free from any unwanted residue.
- Deodorization: This final stage removes volatile compounds and odors from the palm oil. Specific equipment like deodorization columns is employed to achieve the desired level of odor removal. This stage is crucial in improving the sensory properties and the overall quality of the final palm oil product.
Efficiency and Cost Comparison
A comparative analysis of the efficiency and cost of different bleaching equipment is essential for optimal process design. The table below illustrates a potential comparison, highlighting the trade-offs between capital expenditure and operational costs. Different parameters, such as throughput, energy consumption, and maintenance costs, are critical in evaluating the total cost of ownership.
While various methods exist for bleaching palm oil, achieving a consistent, high-quality result often requires meticulous control over the process. The chemical composition of palm oil and its subsequent processing significantly influence the final product’s properties, a process that, when carefully executed, results in a refined oil. Understanding the nuances of palm kernel oil’s effects on skin, as detailed in this resource on palm kernel oil skin , is also critical for evaluating the broader implications of palm oil processing.
Ultimately, the efficacy of any bleaching method for palm oil hinges on precise control and adherence to established standards.
Equipment Type | Efficiency (Removal Rate %) | Capital Cost (USD) | Operational Cost (USD/Ton) |
---|---|---|---|
Filter Presses | 85-90 | 50,000-200,000 | 1.50-2.50 |
Centrifuges | 90-95 | 100,000-500,000 | 1.00-2.00 |
Bleaching Earth Reactors (Continuous) | 92-98 | 200,000-1,000,000 | 0.75-1.50 |
Schematic Diagram of Bleaching Process Flow
The following schematic diagram illustrates the overall flow of the palm oil bleaching process. The diagram visually represents the different stages and the equipment involved, highlighting the sequential nature of the process.
[A detailed schematic diagram would be presented here if visual representation were allowed.]
Note: The diagram would illustrate the flow of palm oil through pre-treatment, bleaching earth reactors, washing/filtration, and finally, deodorization stages. Key equipment like filter presses, centrifuges, and heating/cooling systems would be visually represented in their respective locations within the process.
Bleaching Process Steps
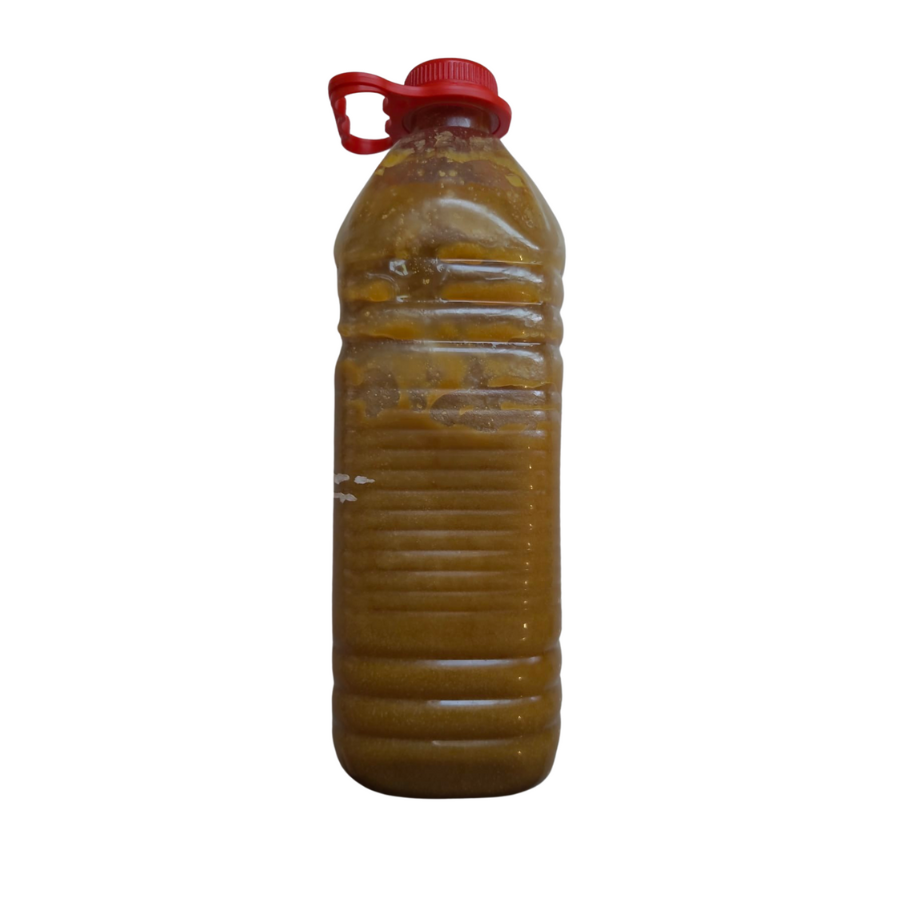
Palm oil bleaching is a crucial refining step that significantly impacts the final product’s quality and marketability. The process removes impurities and undesirable colors, leading to a consistent, light-colored product suitable for various applications. Efficient bleaching is essential for maximizing yield and meeting stringent industry standards.
The bleaching process involves a series of carefully controlled steps, each designed to eliminate specific impurities while maintaining the oil’s desirable properties. The precise temperature, time, and contact with bleaching agents directly influence the effectiveness of each step and the quality of the final product. Variations in these parameters can significantly affect the color, clarity, and overall quality of the bleached palm oil.
Washing and Pre-treatment
The initial steps of the bleaching process are crucial for ensuring efficient removal of impurities. Washing removes any residual water or solids from the crude palm oil. Pre-treatment stages, such as degumming, are performed to remove natural gums and other interfering substances that could interfere with the bleaching process. This pre-treatment ensures the bleaching agents have optimal contact with the target impurities.
Contact with Bleaching Agents
The palm oil is then brought into contact with bleaching agents, typically activated earth (e.g., clays, diatomaceous earth) or other specialized bleaching agents. These agents adsorb impurities, removing unwanted colors and odor. The specific type of bleaching agent employed will depend on the desired quality of the final product and the characteristics of the crude palm oil. This stage typically involves controlled agitation to ensure even distribution of the bleaching agents throughout the oil.
Filtration
Filtration is a critical step in the bleaching process, separating the bleached oil from the spent bleaching earth. Sophisticated filtration systems are used to remove the bleaching agents, ensuring that no residue remains in the final product. The effectiveness of the filtration process directly affects the final product quality, as any residual bleaching agent can negatively impact the taste, color, and odor of the bleached palm oil. Proper filtration ensures the product meets the standards required for various applications, from food-grade products to industrial uses.
Drying and Deodorization
After filtration, the bleached palm oil is dried to remove any remaining moisture. Drying ensures that the final product meets the required moisture content standards. This step is critical to prevent microbial growth and maintain the stability of the product. Subsequently, deodorization is performed to eliminate any undesirable odors or flavors. Deodorization is typically conducted at elevated temperatures and under vacuum conditions, allowing for the removal of volatile compounds. Careful control of the temperature and time parameters is crucial to avoid unwanted changes in the oil’s quality. Variations in drying and deodorization parameters can affect the product’s final color, odor, and flavor profile. For instance, excessive heat during drying can result in a darker or altered flavor.
Final Product Quality Control
The final quality control measures involve testing the bleached palm oil for various parameters, including color, clarity, free fatty acids, and moisture content. The results of these tests determine if the bleached palm oil meets the required specifications. These tests are crucial in ensuring consistent product quality and adherence to industry standards. Variations in the quality control parameters can lead to rejection of the product or necessitate adjustments in the bleaching process. Strict quality control procedures help maintain consistent product quality, ensuring that the final product is fit for its intended use.
Raw Material Considerations
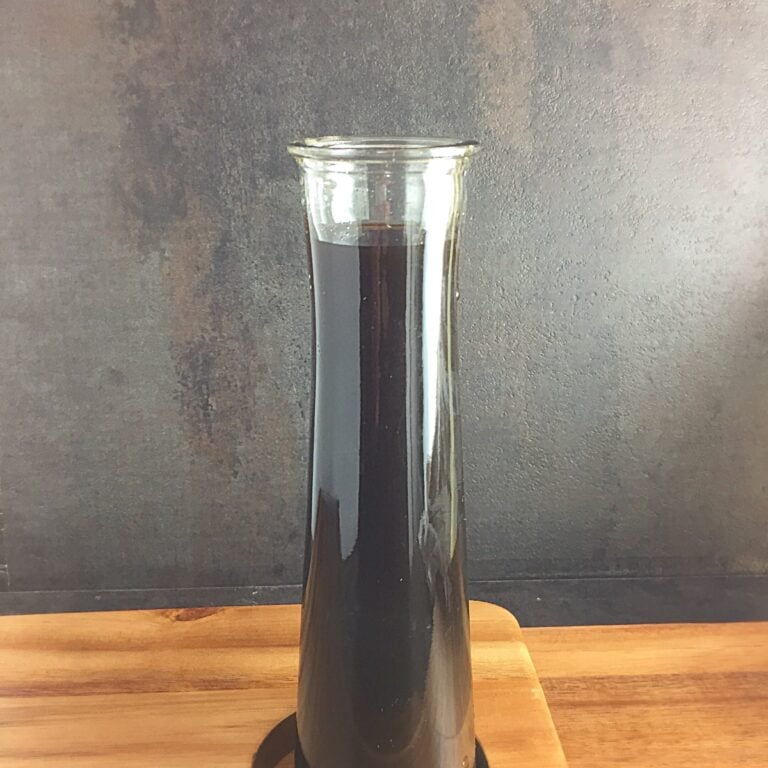
The quality of palm fruit, the raw material, profoundly impacts the efficiency and cost-effectiveness of the bleaching process. Variations in fruit ripeness, oil content, and contaminants directly influence the bleaching outcome and the final product’s quality. Understanding these factors is crucial for optimizing the process and ensuring a consistent, high-quality bleached palm oil product.
The efficiency of the bleaching process is significantly tied to the raw material’s characteristics. Factors like the presence of impurities, the degree of oil content, and the level of fiber content in the fresh fruit pulp will all directly impact the bleaching procedure’s efficacy. Proper pre-treatment of the raw material before bleaching is essential to minimize the amount of impurities that can hinder the bleaching process and ultimately affect the quality of the final product.
Impact of Raw Material Quality on Bleaching Process, How to bleach palm oil
The quality of the raw palm fruit significantly affects the bleaching process’s effectiveness and the quality of the final product. Factors like fruit ripeness, presence of impurities, and oil content in the fruit directly influence the bleaching process’s success. For instance, underripe fruit often contains a higher concentration of undesirable compounds that can hinder the bleaching process, leading to lower efficiency and a lower-quality bleached oil. Conversely, overripe fruit might have a higher level of free fatty acids, which can affect the stability of the bleached palm oil and create off-flavors.
Factors Influencing Bleaching Efficiency
Several factors linked to the raw material significantly influence the bleaching process’s efficiency. These include the presence of undesirable compounds in the fresh fruit pulp, such as pigments, waxes, and gums. The amount of oil content in the fruit pulp directly correlates to the amount of oil needing bleaching. Higher fiber content in the pulp necessitates more processing steps, potentially increasing costs and time. The presence of water or moisture in the raw material can affect the absorption and effectiveness of the bleaching agents, requiring additional pre-treatment steps.
Importance of Pre-Treatment
Proper pre-treatment of the raw material is critical for the success of the bleaching process. Pre-treatment steps aim to remove impurities, such as fibers, water, and other unwanted materials, before the bleaching process begins. This improves the efficiency of the bleaching process by reducing the load on the bleaching agents and equipment. Furthermore, effective pre-treatment helps ensure that the bleaching agents can more effectively interact with the oil, minimizing the chances of leaving behind impurities.
Effects of Different Raw Material Types on Final Product
Different types of palm fruit can yield different qualities of bleached palm oil. For instance, fruits from a specific region might have varying levels of impurities or pigments. This variation directly impacts the color, clarity, and overall quality of the final product. Furthermore, the level of free fatty acids in the raw material can affect the final product’s stability and shelf life. Differences in the raw material also impact the bleaching process’s cost-effectiveness, as some types may require more pre-treatment steps or higher amounts of bleaching agents to achieve the desired quality. This means that consistent quality control and adjustments in the bleaching process are essential to maintain product quality across different harvests.
Quality Control During Bleaching
Rigorous quality control (QC) is paramount in the palm oil bleaching process. Maintaining consistent product quality, meeting industry standards, and ensuring consumer safety are crucial for a successful operation. This stringent approach ensures the final product meets the desired specifications, thereby maximizing profitability and market competitiveness.
Effective QC measures are implemented throughout the bleaching process, from the initial raw material assessment to the final product analysis. This meticulous monitoring allows for immediate identification and correction of any deviations, safeguarding the integrity of the bleached palm oil.
Monitoring Specific Parameters
Thorough monitoring of critical parameters during each stage of bleaching is essential. This encompasses factors such as the concentration of bleaching agents, the duration of the bleaching process, and the temperature at which the process is conducted. Variations in these parameters can significantly impact the final product quality. Accurate measurements of these variables are vital to maintain consistency and achieve the desired bleaching efficacy.
Assessment Methods
Several methods are employed to assess the quality of the bleached palm oil. These methods include physical evaluations, chemical analyses, and sensory assessments.
- Physical Evaluations: Visual inspection, such as assessing the clarity and color of the oil, is a fundamental step. The presence of any unusual precipitates or suspended particles can indicate process deviations. Furthermore, the viscosity and consistency of the bleached oil are also carefully monitored.
- Chemical Analyses: Sophisticated laboratory tests are conducted to determine the oil’s free fatty acid (FFA) content, peroxide value (POV), and other critical chemical properties. These tests provide objective data on the oil’s purity and stability. Specific standards, like those set by the International Organization for Standardization (ISO), guide the acceptable ranges for these parameters. For example, an elevated FFA content may signify incomplete neutralization during the process.
- Sensory Assessments: Trained personnel assess the bleached palm oil’s aroma, taste, and overall quality. These sensory evaluations complement the objective data from physical and chemical analyses, providing a holistic view of the product’s characteristics. Any unusual odor or taste might signal contamination or an undesirable reaction.
Impact on Final Product Characteristics
Quality control directly impacts the final product’s characteristics. Consistent monitoring ensures the bleached palm oil meets the desired color, clarity, and stability. This, in turn, influences the product’s suitability for various applications, such as food processing and cosmetics. Furthermore, maintaining high quality ensures a longer shelf life and reduces the likelihood of rancidity or other quality degradation. For instance, consistent bleaching minimizes the presence of undesirable compounds, resulting in a product suitable for sensitive food applications.
Environmental Impact of Bleaching
Palm oil bleaching, while crucial for refining and achieving desirable qualities, carries environmental implications. The process, though often optimized for efficiency, generates waste streams and potentially introduces pollutants into the ecosystem. Understanding these impacts is critical for developing sustainable bleaching practices and mitigating negative consequences.
Waste Generation and Disposal
Bleaching palm oil typically involves the use of chemical agents and processes that generate significant waste products. These include spent bleaching earth, which is often a large volume of material. Disposal of these wastes is a major concern, requiring careful consideration. Improper disposal can contaminate water sources and soil, impacting local ecosystems and human health. Effective waste management systems, including controlled landfills or specialized treatment facilities, are essential to minimize environmental risks. Regulations and industry best practices are needed to ensure safe and environmentally responsible waste handling.
Potential Risks of Bleaching Agents
The selection of bleaching agents significantly impacts the environmental footprint of the process. Certain chemicals, while effective in removing impurities, pose risks if not handled and disposed of appropriately. For instance, chlorine-based bleaching agents can introduce harmful byproducts into the wastewater, leading to water contamination. Alternatives like chlorine dioxide or ozone-based bleaching agents, while less harmful, also need careful management to avoid unintended environmental consequences. Responsible chemical selection and strict adherence to safety protocols are crucial to minimize risks.
Sustainability Practices in Palm Oil Bleaching
Sustainability in palm oil bleaching requires a multi-faceted approach that considers the entire lifecycle of the process. Innovative bleaching techniques and the use of alternative bleaching agents are being explored to reduce the environmental impact. Some companies are adopting closed-loop systems to minimize waste generation and reuse byproducts. Improved filtration methods and more efficient processing steps contribute to reduced chemical consumption and water usage. Furthermore, the integration of sustainability criteria into procurement and supply chains is essential to ensure the long-term viability and environmental responsibility of palm oil bleaching operations. Sustainable palm oil certifications and industry initiatives are increasingly important in guiding best practices.
Environmental Regulations and Compliance
Governments worldwide are implementing regulations and standards to control the environmental impact of palm oil production and processing, including bleaching. Compliance with these regulations is crucial for businesses operating in this sector. These regulations often mandate specific waste disposal methods, limit the use of certain chemicals, and set emission standards. Palm oil producers must demonstrate compliance with these regulations to maintain operational licenses and ensure consumer confidence. Penalties for non-compliance can be substantial.
Safety Precautions During Bleaching
Palm oil bleaching, while crucial for refining the product, presents inherent safety risks. Proper adherence to safety protocols is paramount to preventing accidents and ensuring a safe working environment. Failure to implement these measures can lead to significant health hazards and costly downtime.
The process involves handling potentially hazardous chemicals, including bleaching agents and caustics, necessitating meticulous precautions. This section Artikels the critical safety measures to mitigate risks during the bleaching procedure.
Hazard Identification
The bleaching process encompasses a range of potential hazards, stemming from the chemicals involved. These hazards include skin and eye irritation, respiratory issues, and fire risks. The handling of bleaching agents, such as chlorine dioxide, requires specific safety procedures. Furthermore, the use of corrosive chemicals, such as sulfuric acid, poses significant dangers if proper handling procedures are not followed.
Personal Protective Equipment (PPE)
Appropriate personal protective equipment (PPE) is critical for minimizing exposure to hazardous materials. This includes but is not limited to:
- Protective Clothing: Full-body protective suits, resistant to chemicals, are essential for workers involved in direct contact with the bleaching agents. These suits should be impervious to the specific chemicals used in the bleaching process.
- Eye Protection: Safety goggles or face shields are mandatory to prevent chemical splashes or vapors from entering the eyes. The type of eye protection should be selected based on the specific hazards present.
- Respiratory Protection: If airborne chemicals or particles are present, respirators are required. The type of respirator must be appropriate for the specific contaminants and their concentrations in the air.
- Hand Protection: Gloves made of chemical-resistant materials are crucial to protect hands from prolonged exposure to the bleaching agents and other chemicals used. The material of the gloves should be carefully selected to match the chemical characteristics of the substances involved.
Emergency Procedures
Implementing effective emergency procedures is vital for swift and appropriate response in case of accidents. These procedures should be well-defined and readily available to all personnel. A comprehensive plan should cover the following aspects:
- Spill Response: Specific procedures for handling chemical spills should be in place. These procedures should detail the steps to contain the spill, neutralize the chemical, and ensure the safety of personnel and the environment. Spill kits containing the necessary materials, including absorbent materials and protective gear, should be readily accessible.
- First Aid: Immediate first aid procedures for chemical exposures are critical. This includes knowing how to decontaminate exposed skin or eyes and administering appropriate first aid based on the type of exposure.
- Evacuation Procedures: A clearly defined evacuation plan, in case of a major incident or uncontrolled release of chemicals, is critical. The plan should include designated evacuation routes, assembly points, and procedures for contacting emergency services.
- Emergency Contact Information: Emergency contact information, including local fire departments, medical personnel, and poison control centers, should be readily available and clearly displayed.
Chemical Handling Procedures
Safe handling of chemicals is paramount. Strict adherence to these procedures minimizes risks.
- Storage: Bleaching agents and other chemicals should be stored in designated areas, away from incompatible materials and ignition sources, following appropriate safety regulations.
- Transportation: Transportation of chemicals should be handled with appropriate containers and procedures to prevent spills or leaks. Transportation should only be done by trained personnel and with the necessary protective gear.
- Mixing Procedures: Mixing chemicals should only be done by trained personnel, following established safety protocols, and using the proper equipment. Care must be taken to prevent accidental reactions or hazardous releases.
Optimization Techniques for Bleaching
Optimizing the palm oil bleaching process is crucial for maximizing yield and minimizing environmental impact. Efficient bleaching not only improves product quality but also reduces operational costs, making it a key focus for industry players. Careful consideration of various factors is essential to achieve these goals.
Improving the efficiency of the bleaching process requires a multi-faceted approach. This involves understanding the factors that influence the process, identifying areas for improvement, and implementing targeted strategies to enhance yield and reduce energy consumption.
Factors Affecting Bleaching Efficiency
Several factors influence the efficiency of the bleaching process. These include the quality of the raw palm oil, the type of bleaching earth used, the operating conditions of the bleaching equipment, and the control of the process parameters. Maintaining consistent quality of the raw material, choosing appropriate bleaching earth, and optimizing process parameters are key for achieving optimal results.
Optimization Techniques to Improve Efficiency and Yield
Several strategies can be employed to enhance the bleaching process’s efficiency and yield. These techniques focus on optimizing process parameters, using advanced bleaching earth, and managing the raw material input effectively.
- Optimizing Process Parameters: Precise control of temperature, pressure, and residence time within the bleaching equipment is essential. Adjusting these parameters based on real-time data and feedback loops can significantly impact the process’s efficiency. For instance, adjusting the residence time to allow adequate contact between the palm oil and the bleaching earth, while minimizing the time for heat exchange, can improve efficiency. Moreover, maintaining a consistent pH throughout the process can optimize the bleaching reaction.
- Advanced Bleaching Earth Selection: Utilizing specialized bleaching earth with improved adsorption capacity and selectivity can enhance the efficiency of the bleaching process. Research into and development of new bleaching earth types, focusing on their specific surface area, pore size distribution, and chemical composition, can result in a more efficient process. For example, the use of activated carbon can be explored to achieve higher removal rates of color and impurities.
- Raw Material Pre-treatment: Proper pre-treatment of the raw palm oil can significantly improve the efficiency of the bleaching process. This includes removing impurities and contaminants from the oil before the bleaching process begins. This pre-treatment can include degumming, neutralization, and deacidification steps to prepare the oil for optimal bleaching.
Reducing Energy Consumption
Minimizing energy consumption is a crucial aspect of optimizing the palm oil bleaching process. Implementing energy-efficient technologies and processes can substantially reduce operational costs and environmental impact.
- Energy-efficient Equipment: The use of energy-efficient pumps, heaters, and other equipment can reduce energy consumption significantly. Investing in modern equipment with high energy efficiency ratings is vital.
- Process Optimization: Optimizing the process parameters, including temperature and residence time, can reduce the energy required for heating and cooling. Heat recovery systems can also be implemented to capture and reuse waste heat.
- Improved Insulation: Implementing improved insulation in the bleaching equipment can reduce heat loss and minimize energy consumption for maintaining optimal temperature.
Summary of Optimization Strategies
Optimization Strategy | Potential Benefits |
---|---|
Optimizing Process Parameters | Improved efficiency, reduced processing time, higher yield, and minimized energy consumption. |
Advanced Bleaching Earth Selection | Enhanced color and impurity removal, improved oil quality, and reduced bleaching earth usage. |
Raw Material Pre-treatment | Reduced processing time, improved efficiency, and minimized loss of oil quality. |
Energy-efficient Equipment | Lower energy costs, reduced environmental impact, and improved operational efficiency. |
Process Optimization | Reduced energy consumption for heating and cooling, and increased efficiency of the bleaching process. |
Improved Insulation | Reduced heat loss, minimized energy consumption, and improved operational efficiency. |